We have noticed an increase in the amount of calls to our office relating to water permeation and damage on new construction (buildings only 1-3 years old). You would not think that new buildings would have such issues but we have considerable evidence to the contrary. In fact, we are providing you with two recent articles (one from the Chicago SunTimes and one from the Chicago Tribune) remarking on how prevalent these problems are.
Undoubtedly these leaking issues derive from initial workmanship flaws coupled with an inferior building material. Summer months can bring temperatures as high as 120 degrees on block walls which are directly exposed to the sun. Block walls exposed to the wind, snow and ice can drop the wall temperature to 20 or 30 degrees below zero. These temperature extremes expand and contract the block units creating small hairline cracks within the mortar joints and often within the block themselves. If water penetrates these cracks and freezes the cracks get larger. This pattern is repeated every freeze/thaw cycle. The same thing happens during the settling of a newly constructed block wall building. As the new foundation shifts it puts pressure on different areas of the building causing structural cracks within the mortar joints. Vibration from traffic and construction also puts stress on the block facade exacerbating the cracking of the mortar joints.
To combat these complaints Arrow Masonry has devised a preventative maintenance program addressing each new construction problem and its solution. The following photos illustrate these serious workmanship concerns.
Split Face Block Repair Images
Split Face Block Construction Problems:
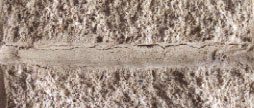
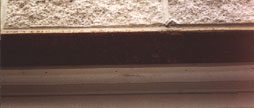
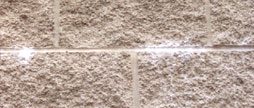
Split Face Block Construction Solutions:
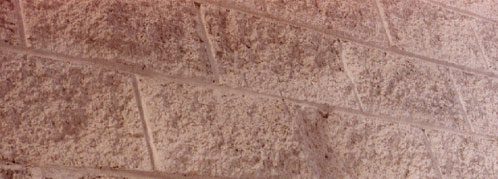
In order to stop the water penetrating problem on this building, Arrow Masonry had to first grind out all vertical and horizontal mortar joints. All ground out joints were primed with a caulk primer then sealed and tooled with a polyurethane caulk to match the existing color and profile of the original joints. Once the mortar joints were sealed, the block itself needed to be waterproofed. Arrow Masonry chose to use an elastometric coating (a heavy duty rubberized paint which can be tinted to match the color of the block) due to the extreme leaking. This particular method repels water most effectively on split face block and comes in a variety of colors.